Total decontamination duration: 3 days
Validation: 6-log reduction via 3rd party microbiology lab
Sterilant: Hydrogen Peroxide
Delivery: Atomizing nozzle
It is common practice that before a Specified Pathogen Free (SPF) facility is handed over to owner after construction to perform a facility decontamination. This will ensure when the animal models are moved in, there is a low risk of being contamination by the environment.
This 2000 square meters (sqm) SPF facility was designed to house both small and large animal models. Within this large facility is a labyrinth of rooms and corridors with segregations of procedure and holding rooms.
Our team worked with the owner in planning the decontamination by zones. Safety considerations include worker safety and eliminate possibility of leakage. Zoning of the facility is important so that when a designated area has been decontaminate, there will be no ‘walk-through’ where contaminants may be reintroduced.
Strategy:
2 sets of 3 Dry Fogging nozzles were deployed for this facility. Typically 3 nozzles will be able to cover about 250sqm or more depending on the layout i.e. if the room is ‘L’ shaped or rooms with possible ‘dead corners’. As the first set is performing decontamination, the second set is being deployed for preparation. Upon completion of the decontamination cycle within 2 hours (preparation time included) , the second set is then activated for decontamination. The first set is then being retrieved and deploy to the third zone for decontamination preparation. In a workday, about 3 cycles of decontamination can be performed. For a 2000 sqm facility, the total number of days to complete the decontamination was about 3 days on site.
The actual decontamination cycle i.e. Gassing, Holding and Aeration can be performed within 1 hour. Thanks to the nozzle technology, lesser concentration of Hydrogen Peroxide is being introduced. This contributes to much lesser time needed for the aeration stage to achieve 1ppm STEL for Hydrogen Peroxide before it is safe for re-entry.
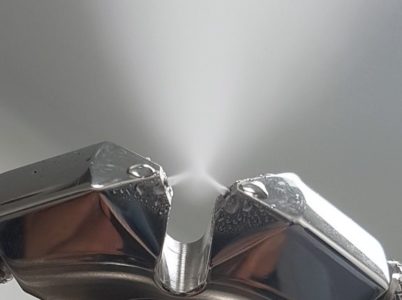
Total decontamination duration: 14 days
Validation: Chemical Indicator with 1micro-gram of Beta Lactam to be deactivated to less than 1 nano-gram. Detection by Gas Chromatography by 3rd party laboratory
Sterilant: Chlorine Dioxide
Delivery: Gaseous
Beta Lactam is the active ingredient for Antibiotics. It is usually manufactured in large quantity in a pharmaceutical API (Active Pharmaceutical Ingredient) facility. Itis known to elicit serious autoimmune response from people who are allergic, even death. As such, responsible pharmaceutical companies will want to ensure that before an API plant is shut down from producing Beta Lactam, an inactivation decommissioning process is in place.
Our team were appointed to perform a full facility deactivation. Scope of works include production area, API processing equipment and mechanical equipment including the ductwork. As many of these facilities are dated, preparation is challenging. Not all mechanical equipment can be accessed easily. Nor was it designed to facilitate deactivation activities.
As such, precise planning, execution and communication with plant engineers are absolutely critical. Activities may include slight modification in the ductwork with proper safety precaution to prevent exposure. HVAC knowhow is a must for our team to safety execute these works.
Strategy:
Deactivation in the ductwork are performed by sections. Locations for insertion of Chemical Indicators are approved by plant engineers. Mechanical equipment located in inaccessible location have to be accessed via scaffolding. Work are being conducted safely with full PPE. Some equipment may be isolated and deactivated on its own. All decisions and actions are documented to GMP standard and serve as part of the report. Since all API plants are designed differently all over the world, pre-work site survey will highlight potential issues with our team’s proposed solution. Validation is the ultimate indication that deactivation is being conducted correctly.
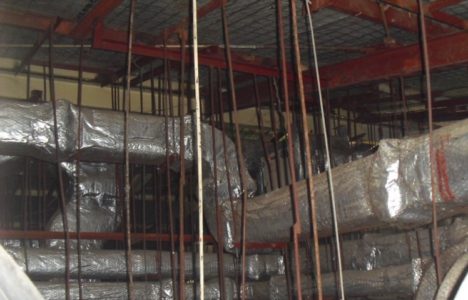
Total decontamination duration: 1 day
Validation: 6-log reduction via 3rd party microbiology lab
Sterilant: Hydrogen Peroxide with Peracetic Acid 0.5%
Delivery: Atomizing nozzle
It is important that the medical device manufacturing environment is immaculate and free from contamination. Environment bio-burden reduction is regularly implemented to meet this objective. Consequences can be substantial if products are found to be contaminated or there is an increased risk of contamination during manufacturing process.
Since manufacturing plant is on-going with scheduled shutdown for maintenance of the facility, a quick turnaround for this bio-burden reduction exercise is highly appreciated to facilitate other activities in the limited shut down window.
Strategy:
Our team suggested hydrogen peroxide with 0.5% of peracetic acid. The introduction of a small ppm of peracetic acid compliments the sterilant capability of H2O2. It can achieve efficacy even within a 4oC fridge for 6 log reduction. It is ideal if an environment contains soil load of bio-material.
The total time taken for the 1000 sqm was around an hour for the whole decontamination cycle. Preparation time was about 0.5 day. Validation was conducted via 6-log Biological Indicators and tested by a third party microbiology lab.
Total decontamination duration: 3 days
Validation: 6-log reduction via 3rd party microbiology lab
Sterilant: Hydrogen Peroxide
Delivery: Atomizing nozzle
It is common practice that before a Specified Pathogen Free (SPF) facility is handed over to owner after construction to perform a facility decontamination. This will ensure when the animal models are moved in, there is a low risk of being contamination by the environment.
This 2000 square meters (sqm) SPF facility was designed to house both small and large animal models. Within this large facility is a labyrinth of rooms and corridors with segregations of procedure and holding rooms.
Our team worked with the owner in planning the decontamination by zones. Safety considerations include worker safety and eliminate possibility of leakage. Zoning of the facility is important so that when a designated area has been decontaminate, there will be no ‘walk-through’ where contaminants may be reintroduced.
Strategy:
2 sets of 3 Dry Fogging nozzles were deployed for this facility. Typically 3 nozzles will be able to cover about 250sqm or more depending on the layout i.e. if the room is ‘L’ shaped or rooms with possible ‘dead corners’. As the first set is performing decontamination, the second set is being deployed for preparation. Upon completion of the decontamination cycle within 2 hours (preparation time included) , the second set is then activated for decontamination. The first set is then being retrieved and deploy to the third zone for decontamination preparation. In a workday, about 3 cycles of decontamination can be performed. For a 2000 sqm facility, the total number of days to complete the decontamination was about 3 days on site.
The actual decontamination cycle i.e. Gassing, Holding and Aeration can be performed within 1 hour. Thanks to the nozzle technology, lesser concentration of Hydrogen Peroxide is being introduced. This contributes to much lesser time needed for the aeration stage to achieve 1ppm STEL for Hydrogen Peroxide before it is safe for re-entry.
Total decontamination duration: 14 days
Validation: Chemical Indicator with 1micro-gram of Beta Lactam to be deactivated to less than 1 nano-gram. Detection by Gas Chromatography by 3rd party laboratory
Sterilant: Chlorine Dioxide
Delivery: Gaseous
Beta Lactam is the active ingredient for Antibiotics. It is usually manufactured in large quantity in a pharmaceutical API (Active Pharmaceutical Ingredient) facility. Itis known to elicit serious autoimmune response from people who are allergic, even death. As such, responsible pharmaceutical companies will want to ensure that before an API plant is shut down from producing Beta Lactam, an inactivation decommissioning process is in place.
Our team were appointed to perform a full facility deactivation. Scope of works include production area, API processing equipment and mechanical equipment including the ductwork. As many of these facilities are dated, preparation is challenging. Not all mechanical equipment can be accessed easily. Nor was it designed to facilitate deactivation activities.
As such, precise planning, execution and communication with plant engineers are absolutely critical. Activities may include slight modification in the ductwork with proper safety precaution to prevent exposure. HVAC knowhow is a must for our team to safety execute these works.
Strategy:
Deactivation in the ductwork are performed by sections. Locations for insertion of Chemical Indicators are approved by plant engineers. Mechanical equipment located in inaccessible location have to be accessed via scaffolding. Work are being conducted safely with full PPE. Some equipment may be isolated and deactivated on its own. All decisions and actions are documented to GMP standard and serve as part of the report. Since all API plants are designed differently all over the world, pre-work site survey will highlight potential issues with our team’s proposed solution. Validation is the ultimate indication that deactivation is being conducted correctly.
Total decontamination duration: 1 day
Validation: 6-log reduction via 3rd party microbiology lab
Sterilant: Hydrogen Peroxide with Peracetic Acid 0.5%
Delivery: Atomizing nozzle
It is important that the medical device manufacturing environment is immaculate and free from contamination. Environment bio-burden reduction is regularly implemented to meet this objective. Consequences can be substantial if products are found to be contaminated or there is an increased risk of contamination during manufacturing process.
Since manufacturing plant is on-going with scheduled shutdown for maintenance of the facility, a quick turnaround for this bio-burden reduction exercise is highly appreciated to facilitate other activities in the limited shut down window.
Strategy:
Our team suggested hydrogen peroxide with 0.5% of peracetic acid. The introduction of a small ppm of peracetic acid compliments the sterilant capability of H2O2. It can achieve efficacy even within a 4oC fridge for 6 log reduction. It is ideal if an environment contains soil load of bio-material.
The total time taken for the 1000 sqm was around an hour for the whole decontamination cycle. Preparation time was about 0.5 day. Validation was conducted via 6-log Biological Indicators and tested by a third party microbiology lab.